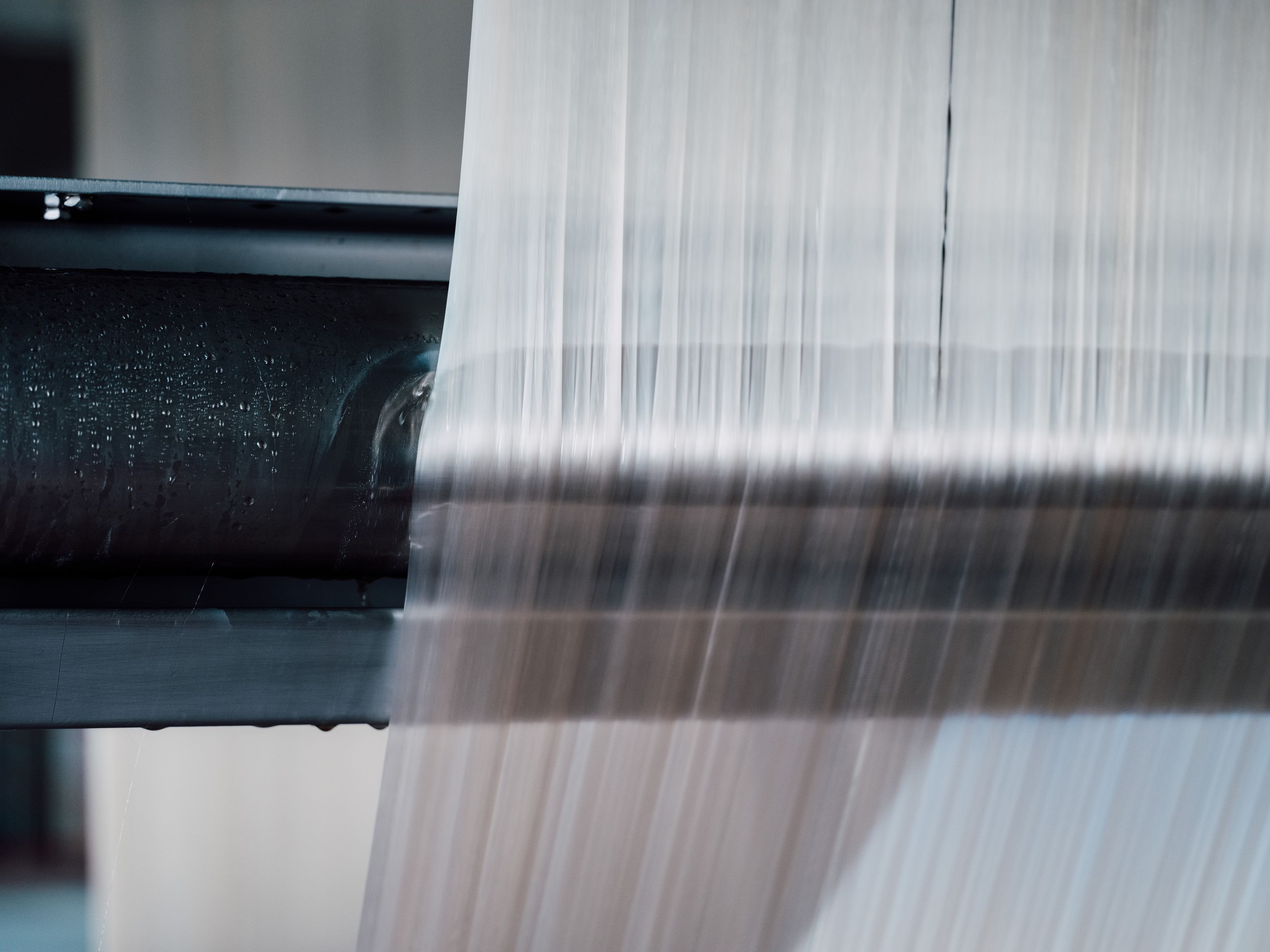
Technologies
Lenzing’s advanced technologiestransforming wood into better fibers
About our technologies
Lenzing's fibers are derived from cellulose − the main component of plants. Our cellulose comes from trees, who build it using sunlight, water, and CO₂. This makes wood an ideal renewable raw material for producing aesthetic and functional fibers.
Drawing on over 80 years of expertise as a global leader in regenerated cellulose fibers, we employ advanced technologies that maximize resource efficiency.
Our production process has two distinct stages. First, we convert wood into pulp − using our biorefinery concept that ensures 100% utilization of wood components. Next, we transform this pulp into high-performance fibers: lyocell, modal, and viscose.
Pulp production – from wood to pulp
Fiber production – from pulp to fiber
Technology-driven solutions for enhanced fiber performance
By employing a broad portfolio of technologies, we equip Lenzing fibers with specific properties directly during the production process. This flexibility allows us to tailor our fibers to individual customer needs and adapt them to a wide range of industry requirements.
Technologies
Fiber technologies for textile fibers
REFIBRA™
REFIBRA™ technology builds on the highly efficient production processes of standard LENZING™ ECOVERO™ fibers. Here, we use textile waste as a raw material, in addition to wood. The fibers contain a minimum of 20% recycled material, which is sourced from pre- and post-consumer waste. LENZING™ ECOVERO™ fibers produced with REFIBRA™ technology also meet the Recycled Claim Standard.¹
Micro
Micro technology lets us produce the very finest fibers within our TENCEL™ portfolio, giving textile products notable softness and lightness. Therefore, fabrics made with TENCEL™ fibers produced with Micro technology stand out for their natural comfort and enjoyable sensation and enable the production of lightweight fabrics with a flowing drape, more even textile appearance, and a softer hand.
Indigo Color
Lenzing’s Indigo Color technology directly incorporates color pigments into the fiber during fiber production and, therefore, helps avoid downstream and energy-intensive conventional dyeing processes. A fabric made from these fibers causes 60 percent lower greenhouse gas emissions than conventionally dyed fabrics.²
Eco Filament
With Eco Filament technology, we extend lyocell production from staple fibers to continuous filaments, which combine directly into ready-to-use yarn without requiring spinning. This advancement in wood-based fiber technology leverages our efficient closed-loop production process while maintaining the natural origin of TENCEL™ Lyocell.
Technologies
Fiber technologies for nonwoven fibers
Translucency
Our patented Translucency technology enables production of VEOCEL™ branded lyocell fibers especially for facial sheet masks. Masks made with VEOCEL™ Lyocell fibers become translucent when infused with serum, enabling producers to address consumer expectations for translucency, smoothness, and comfort, thereby setting them apart from others and conferring a distinctive competitive advantage.
Disperse
The Disperse technology can be applied to VEOCEL™ branded lyocell fibers. It enables the production of short cellulose fibers, designed to be used for flushable products where they contribute to high dispersibility and biodegradability. Fabrics produced with VEOCEL™ Lyocell fibers with Disperse technology are compatible with a wide range of lotions, dispersible and flushable.
Micro
Lenzing’s Micro technology can be applied to VEOCEL™ branded lyocell fibers. The Micro technology allows the production of fine cellulose fibers which are best suited for lightweight fabrics with high opacity and great strength.
Dry
With Lenzing’s Dry technology, VEOCEL™ branded lyocell fibers achieve liquid-controlling properties. The fibers are treated with a compound that renders the fiber surface hydrophobic. The fibers can facilitate efficient distribution of fluids, a particularly useful trait in absorbent hygiene products, as it keeps the surface dry and the touch soft, even after contact with body fluids.
Absorbency
The Absorbency technology can be applied to VEOCEL™ branded viscose fibers. VEOCEL™ Viscose fibers with Absorbency technology are produced using a stringently-controlled and state-of-the-art production process, and are tested according to applicable standards to ensure that the fibers are clean and safe. It enhances the performance of tampons by improving efficient liquid absorbency.
¹ Certified by Control Union Shanghai (CU1260548)
² Graph based on “Terinte et al., 2014: Terinte, N., Manda, B.M.K., Taylor, J., Schuster, K.C., and Patel, M. (2014). Environmental assessment of coloured fabrics and opportunities for value creation: spin-dyeing versus conventional dyeing. Journal of Cleaner Production, Vol. 72: 127–138.”; Textile processing steps being similar for Modal and Viscose, therefore savings are based on calculations of fabric production and dyeing via jet dyeing excl. fiber impact.